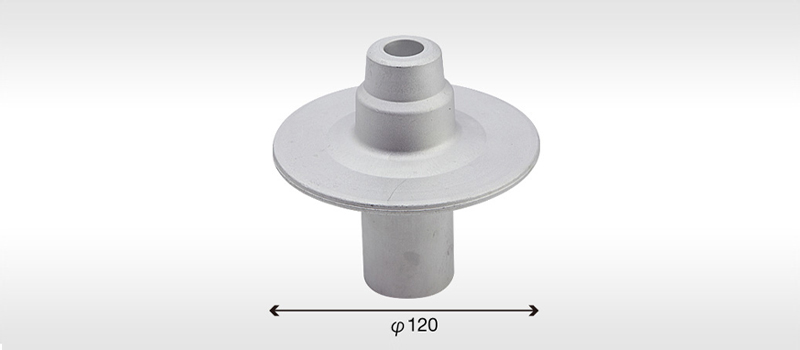
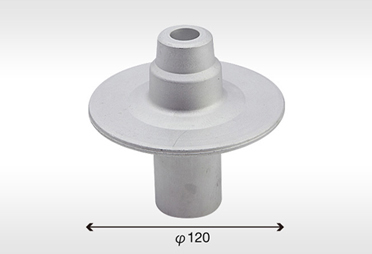
切削から鍛造への工法変更による
<コスト削減を実現する発注方法>
現在、材料から直接削り出している切削部品から、鍛造部品へ製造工法を変更する事により、比較的容易に材料費の大幅削減が可能です。部品形状にも寄りますが、平均約50%の材料費削減を実現できます。
材料費削減幅・約50%の内、約30%は切削工程で発生している無駄な切りくずが、鍛造により発生しなくなるためです【第一の効果】。残りの約20%は、鍛造化に伴い部品の設計を見直し、より薄い形状にすることで(いわゆる「減肉」「薄肉化」)、材料を削減できるためです【第二の効果】。
さらに、鍛造では加工時間も大幅に短縮される(第三の効果)ため、トリプルのコスト削減効果が得られます。
それでは下記に、メーカーの資材発注・担当者様が、スムーズにコスト削減を実現して頂くための鍛造加工業者選びについて、「質問内容」や「技術確認」ポイントを記載いたします。
【質問内容】コスト削減のための「質問」及び「技術確認」ポイント
- 鍛造に変更することで、切削加工の工数を減らすことは可能ですか?
- 切削による加工面を、鍛造加工で同様の精度で仕上げる事は可能ですか?
- 切削部品を鍛造部品に変更することで、必要になる材料費は下がりますか?
- 切削部品を鍛造部品へ変更する際、部品形状を再設計することで材料費を下げられますか?
コスト削減を図る効果的な発注テクニックについて
切削部品を鍛造部品へ変更すれば、材料の靭性(粘り強さ)が高まるため、確実に強度がアップいたします。
それにより、部品の厚みを切削部品より一層薄く仕上げる事が可能になるため、前述の通り部品設計の見直しや、部品構造の効率化・一体化を図る事で、結果、比較的容易にコスト削減を実現できます。
尚、すでに量産中の製品の場合は、部品形状の変更によるコストダウンを図る事は事実上不可能ですが、これから新たに開発する製品の場合は、部品形状の設計を含めて鍛造加工業者と交渉する事で、コスト削減が可能になります。
まずは協力的な鍛造加工業者へ、現状の切削部品の見直しを相談される事をお勧めいたします。
切削部品から鍛造部品への変更により、
約50%のコストダウンを実現
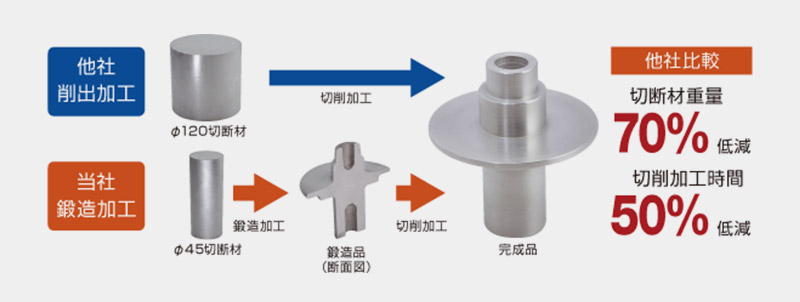
棒材料の切削部品から、鍛造部品に切り替えた事で、
大幅なコスト削減を実現された「ユーザー様事例」をご紹介いたします。
某専門商社K社様では、これまでお客様へ棒材からの切削部品を納入していましたが、そのお客様から大幅なコストダウン要請を受け、解決策を検討しておられました。
そこで白光金属工業では、切削加工から鍛造加工への工法変更をご提案。結果、材料費及び切削加工費が減少、約50%に至る大幅なコストダウンを実現されました。
導入前
切削部品の場合、非常に高価な特殊材を大量に投入していたため、これまで高額の材料費がかかっていました。
導入後
切削部品から鍛造部品への切り替えを決定。その場合工法も全く変わる事で、製品を少ない材料で仕上げる事が可能になり、結果、使用材料が大幅に削減しました。
更に、切削箇所を最小限に加工する事が可能になり、切削加工費のコストも下げる事が出来ました。
【成果詳細】
切削部品から鍛造部品に切り替えた事で、約50%のコストダウンを実現、その際に発生した新たな金型費は、コストダウン効果と合わさって、約半年ほどで回収することが可能になりました。
以降は、約50%のコストダウンを継続、自社の利益率アップに大いに貢献された事例になります。
相談アドバイスを受付いたします
以上、「プロが教える【実践】鍛造発注マニュアル」では、現状部品のコストダウンを検討されたいメーカーの資材発注・担当者様へ、コストダウンを実現させる実践的なサポートを無料で行っております。
現状既に、鍛造加工業者様とのお取引をされている場合でも、丁寧にアドバイスをさせて頂いておりますので、お気軽にお問合せください。
日本の優れたメーカー様の国際競争力アップを実現させるため、これまで半世紀以上にわたる実践経験や豊富な実績、クライアント様の成功実例を基に、スピーディーにご回答、コストダウンを実現可能にする実践的アドバイスを行わせて頂きます。