某金属材料商社様では、つば状の金属部品の製造を切削から鍛造に変更することで、製造コストを30%削減することができました。
- 【課題】切粉が大量に発生し、コスト増を招いている
- 【アドバイス】比較的大型の部品でも、鍛造化が可能
- 【提案】鍛造化により製品強度をアップし、その分薄肉化
- 【成果】材料費削減や工程削減により、30%の大幅なコストダウンに成功
- ここがポイント!
【課題】K社様では、切削加工の際に切粉が大量に発生、
コスト増を招いていることが大きな課題でした
金属材料商社K様では、従来、下図のような「つば状」の特殊合金製部品を切削により製造していましたが、その形状から大量の切粉が発生。実際、完成した製品重量よりも廃棄される切粉の重要が大きいため、以前から問題を感じておられました。
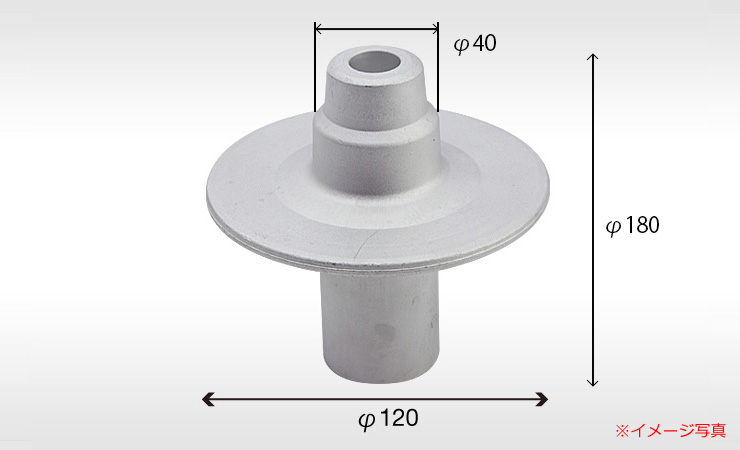
そこへ、工法転換を決定づけたのは、部品納入先からの、大幅なコストダウン要請です。
既存の小手先の手法では、大幅なコストダウン不可能と判断。工法をゼロから見直し、新たな製造方法を模索しておられました。
【アドバイス】比較的大型の部品でも鍛造化が可能とお伝えし、
鍛造への転換を検討されることとなりました
そこで、白光金属工業へご相談いただき、解決方法を探ることとなりました。
今回の製品はφ120×φ180という寸法で、K社担当者様は当初、
「この大きさだと、鍛造に適しているとは思わなかった」
とのこと。
そして、お話をお聞きするうち、次のような課題が明らかになりました。
|
【提案】鍛造化により製品の強度をアップし、
その分、薄肉化を実現する方法をご提案しました
以上のような課題を解決するため、弊社から次のような鍛造方法をご提案しました。
|
これを可能にするのが、弊社の保有する業界最大級1000tプレス機と、精密ダイセットの組み合わせです。
本機と独自の熱間鍛造技術力により、製品重量10kg以上、中空最大径φ120、長さL400までの大型部品鍛造を実現できます。
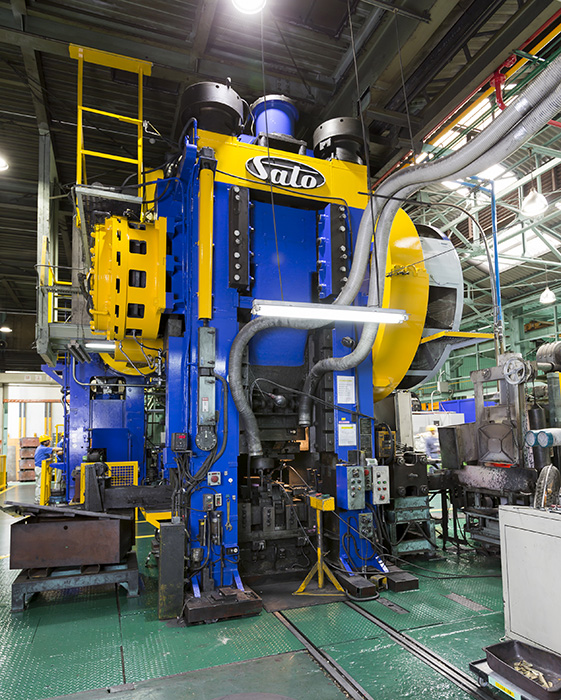
併せて、肉厚を最小限まで薄くできるよう、弊社にて鍛造設計図を作成しました。新たな鍛造形状により、投入重量を削減し、材料費の低減も実現できます。
また、削り代を極力少なく抑えることで、後工程の切削加工を削減。その分の加工費も低減できます。
【成果】30%の大幅なコストダウンに成功しました
その結果として、材料費及び切削加工費で約50%コストダウンという大きな効果を得ることができました。
もちろん、鍛造費及び初期費用として新たに金型費が発生しますが、これについては材料費及び切削加工費の大幅なコストダウン効果により、約半年ほどで償却することが可能になりました。
また、弊社にご注文頂ければ、その後の更新金型費等、追加費用も頂戴しておりませんので、償却後、確実にコストダウン効果が表れています。
最終的には、工法変更品として納入できたことでエンドユーザー様からもご信頼いただき、その後、今回と類似の製品4点もご注文いただきました。
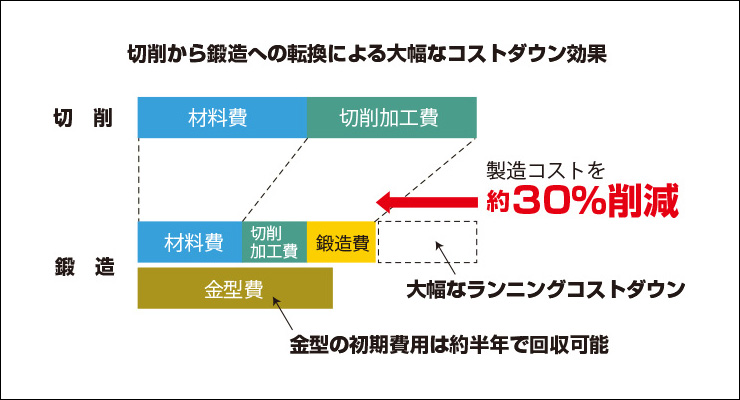
■ここがポイント!
お客様からは、「切削品の鍛造化によって、こんなに大幅なコストダウンが実現できるとは思わなかった」と、お喜びいただいた事例になります。
さらに、弊社では切削加工屑を他の材料と分別し回収していますので、そのままお客様にお返しすることで高価売却が可能となり、さらなる高収益を得ていただくことが可能となっています。
このようなリサイクルにより、環境保全やSDGsへの貢献も達成できました。
白光金属工業では、豊富なノウハウによりこうした課題を解決しています。これからシリーズで 成功事例をご紹介してまいりますので、ぜひご参考になさってください。
コメント