熱間鍛造加工の品質を決める、重要な要素の一つが、材料に対する安定した温度での加熱です。電気による高周波誘導炉を導入することで、鍛造品質の向上はもちろん自動化も実現でき、コストダウンが可能となります。今回は、高周波誘導炉の活用について、分かりやすく解説します。
鍛造における加熱温度の重要性
高周波誘導炉についてお話しする前に、鍛造における加熱温度の重要性について、簡単に触れておきます。
金属は、ある温度以上に加熱すると柔らかくなり、歪んだ結晶が正常な結晶に変化します。これを「再結晶」と言い、「熱間鍛造」とは、この「再結晶温度」以上に熱せられた金属に対して行う鍛造のことを言います。
(ちなみに、この「再結晶温度」以下の常温で成形する鍛造のことを、「冷間鍛造」と呼びます)
熱間鍛造に適した温度は、鉄の場合、一般に1100~1250℃、真鍮は700~750℃、アルミニウムでは400~450℃ぐらいです。鍛造温度がこれより高ければ成形しやすくなりますが、熱により金属材料の物性が変化し、製品に焼き割れが生じることもあります。逆に低ければ、ワークを金型形状通りに変形させることができず、金型を破損することもあり得ます。
したがって、鍛造において、加熱温度が一定のレンジ内に収まるようコントロールすることは、非常に重要と言えます。
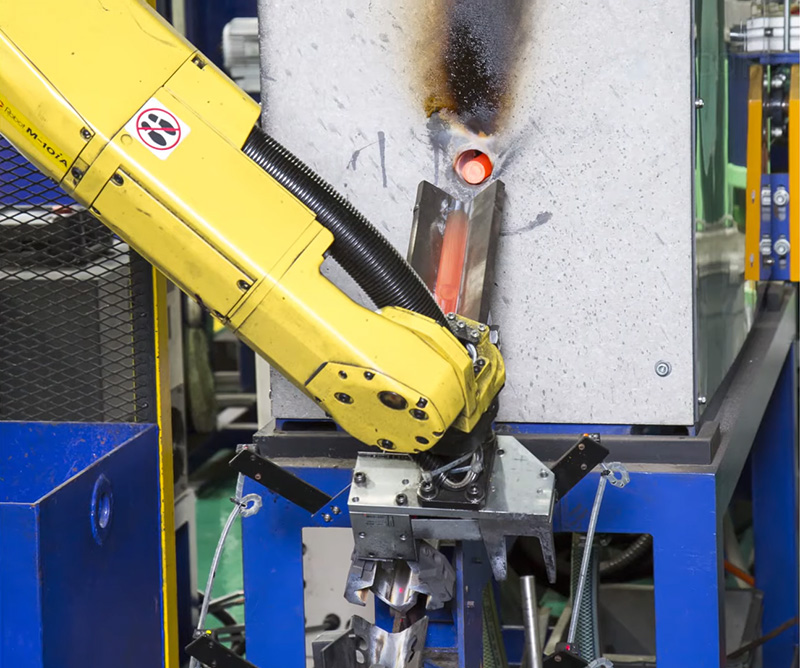
金属別、熱間鍛造に最適な温度は?
材質別に、熱間鍛造に適した温度範囲を表にまとめました。
■熱間鍛造による加熱温度の例
材質 | 温度範囲(℃) |
---|---|
鍛造用アルミ | 340~480℃ |
プレス用マグネシウム | 240~400℃ |
鍛造用黄銅 | 640~800℃ |
チタン | 750~950℃ |
銅 | 800~1050℃ |
炭素鋼 | 800~1250℃ |
ステンレス鋼(18-8) | 750~1150℃ |
マンガン鋼 | 850~1200℃ |
ニッケル鋼 | 850~1150℃ |
ニッケルクロム鋼 | 870~1150℃ |
クロム鋼 | 870~1150℃ |
ニッケル | 850~1250℃ |
モネルメタル | 960~1170℃ |
高周波誘導炉では、上記全ての金属材質に対応することが可能です。
高周波誘導炉による加熱の原理とは?
高周波誘導路が、金属材料を加熱するしくみは、下記のとおりです。
高周波電流の流れる誘導コイルの中に、金属材料(誘導体)を挿入すると、コイルの周りに磁界が発生し、金属棒内に高周波の循環電流(渦電流)が流れます。
この時、金属材料が固有抵抗に応じてジュール熱を発します。これが、高周波誘導炉のしくみです。
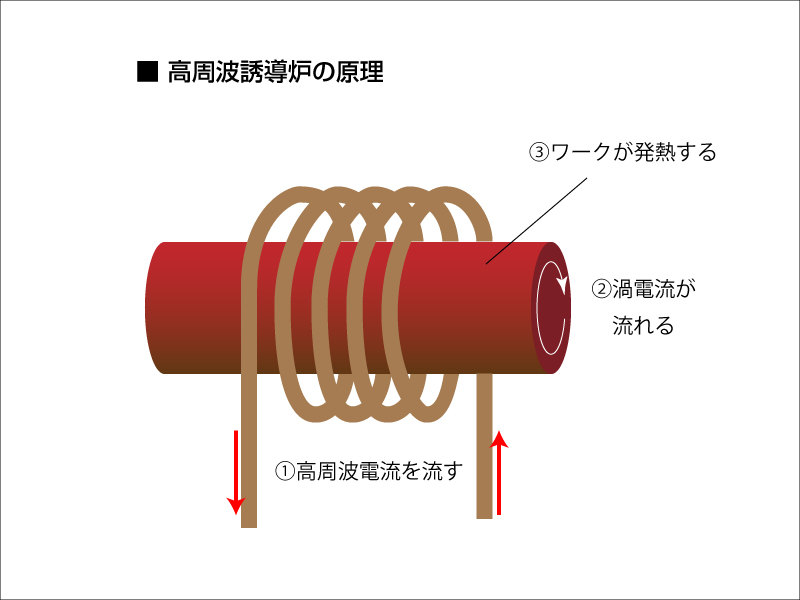
ジュール熱は、抵抗に比例します。つまり、電気を通しやすい銅やアルミは、発熱しにくいわけです。そういう意味で銅は電気誘導炉には適していませんが、アルミは先述の表の通り340~480℃と比較的低い温度で鍛造できるため、十分対応することが可能です。
黄銅は、銅のほか亜鉛が3~4割含まれていますので、これが抵抗を増してスムーズな加熱が得られます。
高周波誘導炉のメリットとは?
1.瞬間加熱が可能
実は、熱間鍛造において瞬間過熱が可能であることは、大きなメリットとなります。加熱した状態で長時間空気に触れていると、材料表面が酸化被膜(黒皮)に覆われてしまい、この状態でプレスを行うと金型の損耗につながる可能性があります。そこで、瞬間過熱を行うことで、酸化被膜の発生を防ぎ、金型損耗によるコスト上昇を抑えることができます。
2.局部加熱が可能
加熱する箇所や範囲、加熱時間を、きめ細かくコントロールできます。材料全体を加熱するのに比べ省エネルギー化が図れ、コストダウンにつながります。
3.クリーン加熱が可能
炎を発さず、ススや排ガスも出ず、工場内の温度上昇を抑えるなど、安全衛生や環境保全にもメリットがあります。
4.加熱温度範囲を自由に設定可能
材料の抵抗値に応じて電流や加熱時間を調整することで、温度範囲を自由に設定することが可能です。
5.高い安全性
直火型ではなくコイル自体は発熱しないため、安全に運用できます。
6.自動化ラインに最適
一定の加熱温度に保つことが難しいガス炉に比べて、高周波誘導炉は電気制御回路により急速かつ安定的に加熱が行えます。また機械を予熱する必要がなく、立上がりが早いため制御し易く、自動化ラインに最適です。
■ここがポイント!
高周波誘導炉の一般的なデメリットとしては、凹凸のある形状は均一に加熱するのが難しい点が挙げられますが、熱間鍛造においてはワークが丸棒材に限られるため問題になりません。
高周波誘導炉は、安定した加熱性能により鍛造品質向上にメリットがあるだけでなく、自動化すなわちコストダウンに欠かせない設備と言えます。
弊社の具体例については、次回記事で詳しくご紹介いたしますので、ぜひご参考になさってください。
コメント