鍛造のコストダウンに直結するのが、工程の自動化・無人化です。
今回は、その中でも生産効率の向上に大きなインパクトを与える、バラ積みピッキングロボットの活用について、分かりやすく解説します。
■ 実はまだ低い、製造業へのロボット導入
まず、ロボット導入の現状について見てみましょう。
ロボットの普及度を示す「ロボット密度」という指標があります。
従業員数に対する、産業ロボットの稼働台数を表すものですが、世界平均は従業員1万人につき約100台、つまり1%に留まっています。
日本でさえ10%割に達しておらず、導入先は自動車産業のような大量生産が主体です。中少量生産におけるロボット化は低いのが実情であり、逆に言えば導入している企業はかなり意欲的な企業と言えます。
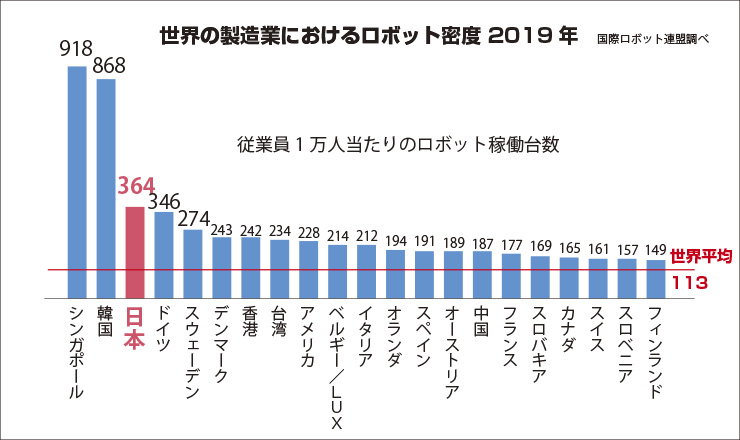
https://ifr.org/ifr-press-releases/news/robot-race-the-worlds-top-10-automated-countries
■ ロボット化のメリット・デメリットとは?
では、ロボット化のメリット・デメリットとは何でしょうか。
ロボット導入のメリットは、次の3点になります。
1.生産性が向上できる
ロボットなら夜間や休日も生産でき、生産性が向上できます。残業代が不要となり、人件費を削減できます。従業員は単純作業から解放され、他の生産性の高い業務に転換することが可能となります。
2.人手不足を解消できる
少子高齢化による人手不足を解消でき、受注量の増加にも対応可能となります。
3.品質が安定化する
人手作業では疲労や不注意によるムラやミスが避けられませんが、ロボットの場合はそれらがないため、製品品質が安定します。また、データ蓄積により不良分析が可能となり品質を改善できるほか、生産量が見通せるので生産計画が立てやすくなります。
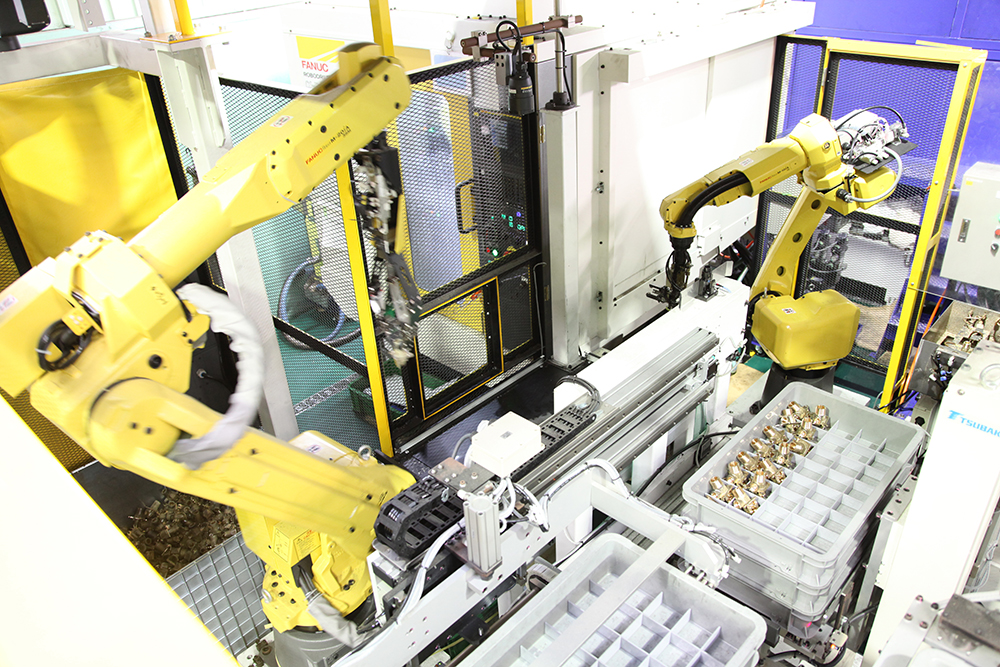
逆に、ロボット化に二の足を踏む要因としては、次のようなものがあります。
1.導入コストがかかる
ロボット本体以外にもロボット周辺装置や、プログラム作成、安全対策費等の導入コストが必要になります。
2.担当者が必要になる
ロボットの調整やメンテナンス等を行うため、ある程度の専門的な知識を持った担当者が必要となります。
3.チョコ停等の発生
故障というレベルでなくても、不具合によるチョコチョコとした生産停止(いわゆる「チョコ停))が、発生する場合があります。
■ 高効率化を実現するばら積みピッキングロボットとは
さて、鍛造に目を移すと、バラ積みされている部品を箱からピッキング(取り出し)して並べる作業は、ロボット化が難しく、従来人手でやらざるを得ないと思われていました。
一見簡単なようですが、人間が部品を取り出す際には、無意識のうちに「目」で見て、「脳」で判断し、「手」を動かすという高度な動作を同時にやっています。
従来のロボットの能力では、バラ積み状態の部品を直接ピッキングするのが困難でした。そのため、ロボットがつかみ易いよう、あらかじめ人の手で部品の向きを揃えて整列させておく必要がありました。
手間をかけないためにロボットを導入しているのに、これではそのメリットが相殺されてしまいます。
そこで、新たに開発されたのが、高効率化を実現する「バラ積みピッキングロボット」です。
人手を介さず、カメラが部品の山を三次元的に検知し、画像処理により個々の部品を認識しながら、一個ずつロボットアームでつかむシステムになっています。
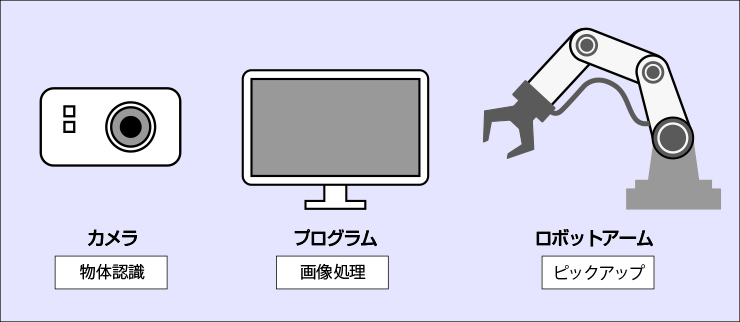
■ 3Dロボットビジョンについて
バラ積みピッキングロボットで、特に画期的な機能は「目」と「脳」です。プロジェクターにより、複数の光のパターンをバラ積みの山に照射し、それを1台または複数のカメラで捉え,三角測量によって対象物までの距離や形状を検知する方法が用いられます。これを、「3Dロボットビジョン」と呼びます。
通常のカメラによるステレオ視のほか、精度の高いレーザ光による三次元計測法があり、カメラとレーザーセンサを組み合わせて認識精度を高めているシステムもあります。
このような高度な画像処理技術により、部品の位置だけでなく、その向きや形状、ピッキングの際に邪魔になりそうな他の部品や箱の位置までも把握することができます。
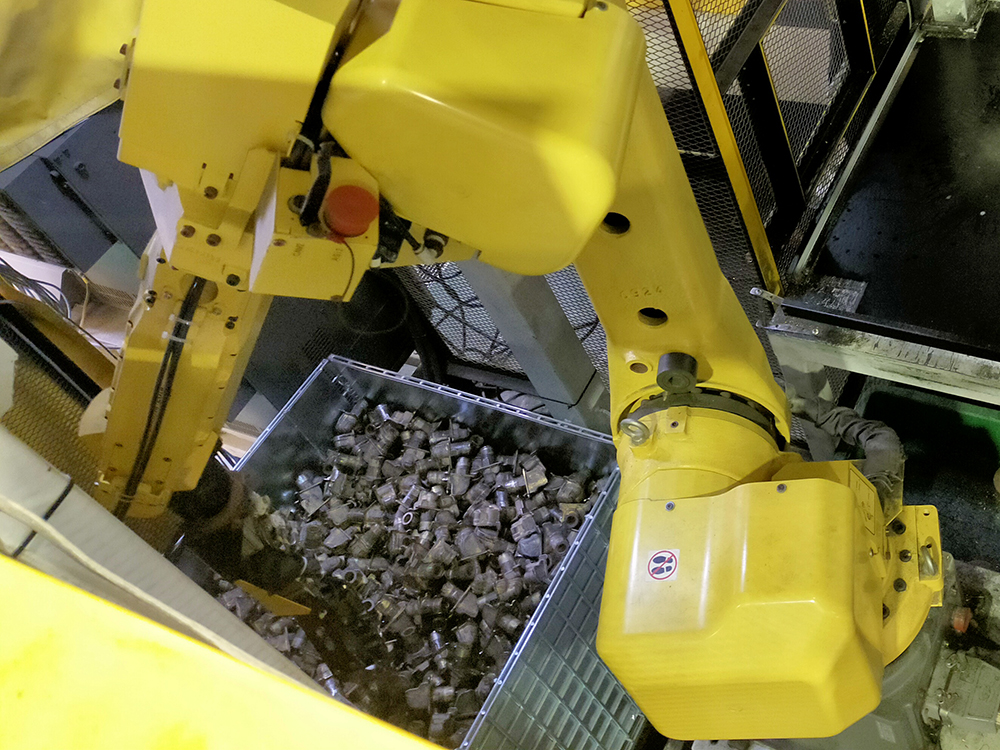
■ ロボットアームについて
3Dロボットビジョンによって得られた3次元情報を基に、ロボットアームは部品をつかみます。
もし、アームの挙動により部品の山が崩れてつかみ損ねた場合は、箱全体を常時モニターすることで変化を察知し、再度軌道を計算してつかみに行くことができます。
■ここがポイント!
ロボットを導入するだけでも人件費大幅コストダウンになるのですが、更にバラ積みピッキング技術を導入することで、効果が倍増します。
また、ピッキングしたワークをもう1台の3Dビジョンカメラで解析してつかみ直すことで、整列させずに定位置で加工機治具にチャッキングすることが可能となり、更なる省人化と品質安定に繋がります。
次回記事では、その実例についてご紹介させていただきますので、参考にしていただければ幸いです。
コメント